The Central Hub for your Well Data and Operations
The Central Hub for your Well Data and Operations
Background
Torc Oil and Gas (Torc) is a 20,000+ BOE/day company with diverse geographic operations. They maintain a combined 10,000 operated and non-operated wells in three separate provinces, Alberta, Saskatchewan and Manitoba. With increasing regulatory challenges, and fewer people to help get the job done Torc looked to software to fill in the gaps.
The Project
Torc is streamlining its operations data in one location. They were looking for a solution that would allow the team to track, enter, store and search data, regardless of department and job title. After some deliberation, the corporate well list was identified as the central hub that connected the different departments and provided the framework to support the operations most operational functions at Torc e.g. HSE Incidents, Maintenance Work, Compliance-based Inspections, Calibrations, Analysis and Well Data. The centrally organized corporate well list also presented the chance for Torc to continue incorporating processes as they came up, e.g. abandonment & reclamation, relying on the existing set of data.
The Challenge
The corporate well data is generally stored in various different places, often with different departments responsible for maintaining and storing critical pieces of information. This results in maintaining redundant datasets, calling into question which data set is correct. Additionally, the inaccessibility of critical well data leads to lost time spent retrieving information.
The current method of storing well data presents the following problems:
-
Dispersed data sets
-
A lack of continuity between departments
-
Little reliability or traceability of the information
-
Continuous attempts to reconcile with the public data
-
Confirming and tracking ever-shifting working interests and cost centres
-
Maintaining Asset retirement obligations
-
Abundant manual entry errors
-
Unavailable data locked into a limited number of seats
While most of this data has been accessible before, it has been hard to view the complete set of data in the same place. Therefore, the primary focus of the muddyboots.online corporate well list was to present all the information in one spot.
The Process
After identifying the Well List as the central connection for all the data, Torc began to collect all their well data and populate muddyboots.online. While more data is being added all the time, Torc had collected a sufficient amount of data to begin using the corporate well list in May 2019. Since then, Torc has worked towards the following objectives:
-
Continuity of information transfer – both between internal departments and external partners. This is especially pertinent in regards to Torc’s diverse geographic operations.
-
The well data cards should be easily accessible to field operators and head office
-
-
Moving the company well spreadsheets to muddyboots.online in attempt to:
-
Reduced data entry errors (limited access to edit)
-
Improve searchability (beyond just the UWI)
-
Sort quickly into relevant data sets such as Non-op and Operated properties.
-
-
Increasing data-driven decisions.
-
Maintaining an up-to-date list of working interest and cost centres.
-
Providing bi-Monthly Reconciliation with public data to help:
-
Ensuring compliance with government regulatory bodies
-
Managing suspended wells and the abandonment process
-
Maintaining internal status on wells for assets in transition
-
-
Building a robust Asset Retirement Obligation process
-
Confirming geographic locations and most recent production data.
-
Increasing the accuracy of measurement schematics.
Above all, Torc has focused on ensuring the centralized corporate well list is used by multiple departments, providing a single source of truth to streamline the company operations.
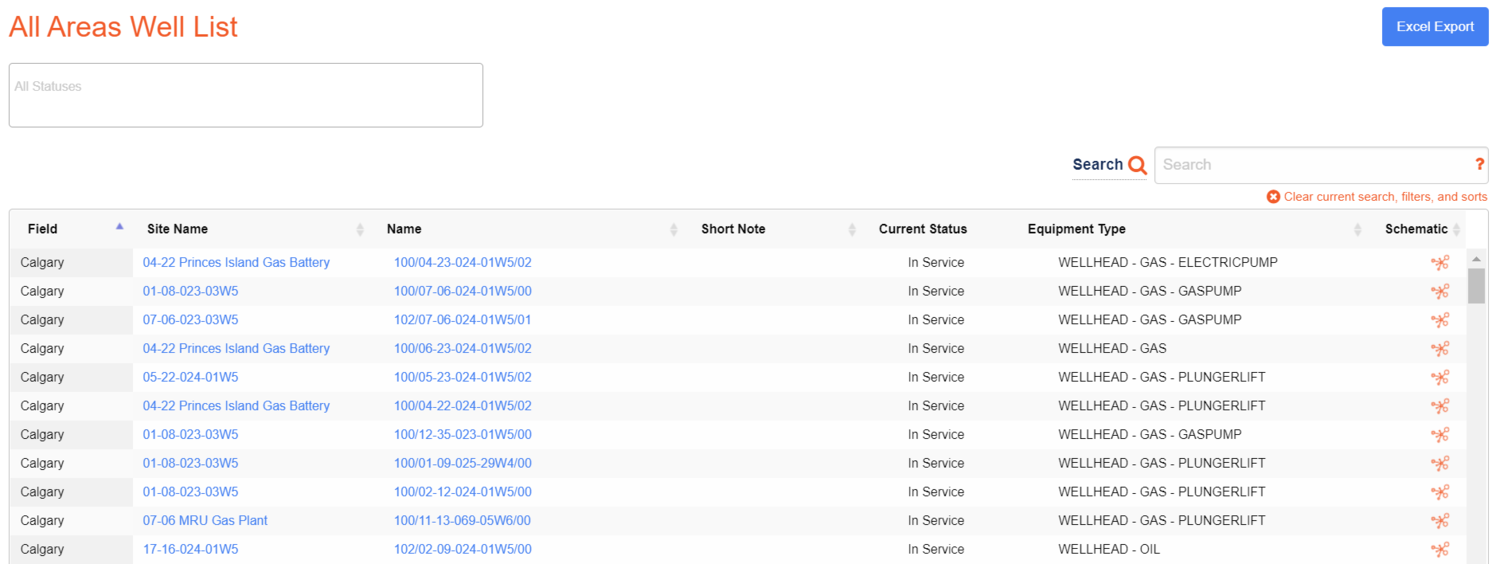
All the details start to come together in the corporate well list main data table.
The Results
While it’s still early days, Torc has seen marked improvements in the following areas:
-
Environmental performance – tracking Torc’s suspended wells and beginning to organize the abandonment process. Ensuring each unique site has a plan as Torc works towards reclamation.
-
Time-saving efficiencies – Torc employees have saved 1-3 hours/day (depending on role) spent tracking down information and are now able to dedicate that time to high value projects.
-
Improved internal communications – the well list allows separate departments to understand the data their way. So, production accounting can find their well site and all the licensing and joint venture information without compromising operations ability to find the wellhead and complete the correct PMs on the equipment.
-
Informed technical decisions – wells data cards are available immediately to each department and can be sorted on key details increasing the number of data-driven decisions. This is especially true of the field operators and shift leads who previously had limited access to the well data cards.
-
Ease of government reporting – by having the information gathered in one place Torc can gather the information needed for various government reporting quickly, regardless of what province they are reporting to.
-
Accessibility of data – cloud-based storage means the information is available when it’s needed. For example, during an external audit, the required details can be gathered right then, no need to follow up with endless email chains and attachments.
-
Decreased windshield time – reliable well statuses allow the operations team to schedule only what is needed decreasing drive time and improving worker safety.
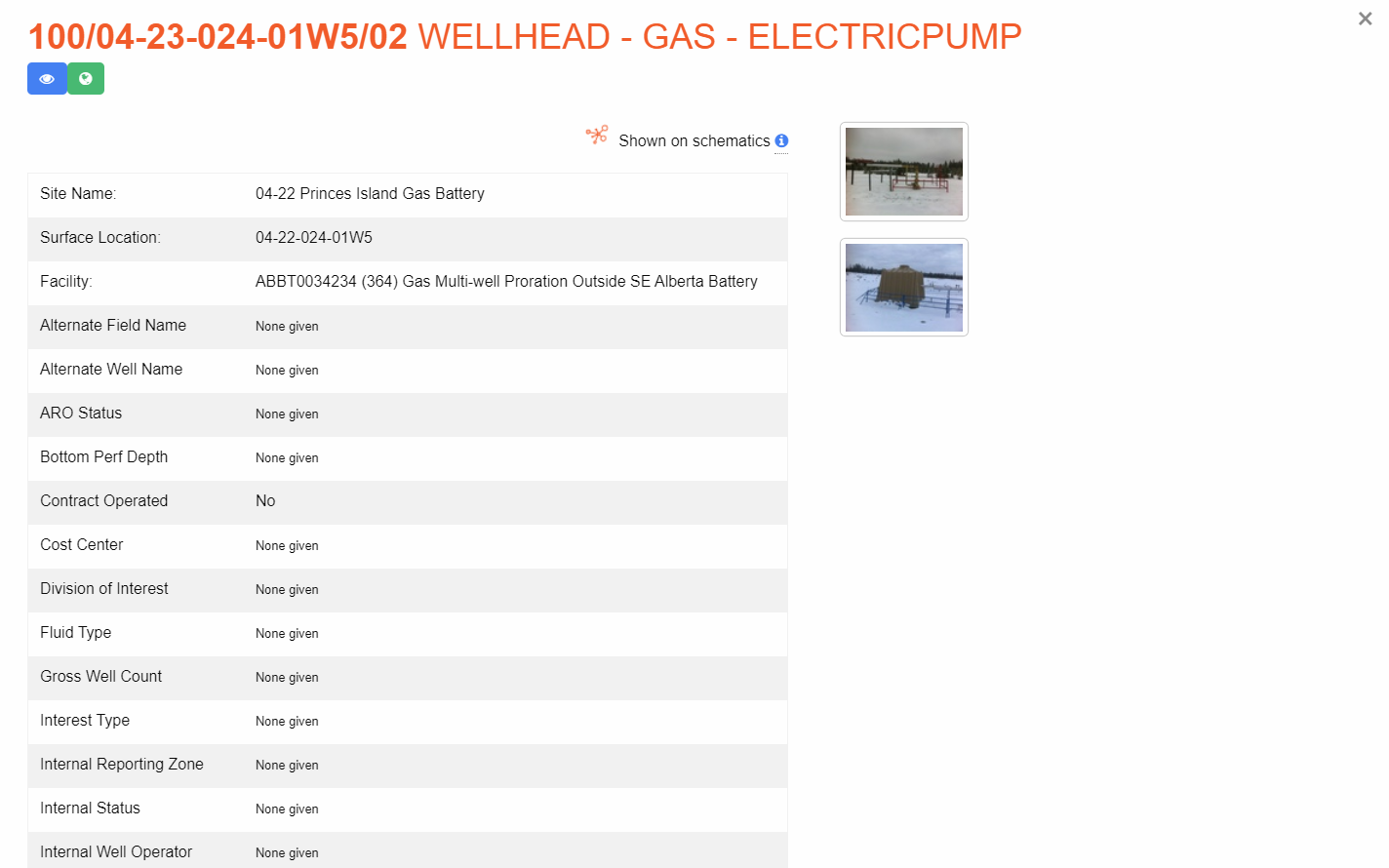
Each wellhead has a comprehensive list of details, allowing many different users to benefit from the corporate well list.
Torc’s focus on making the corporate well list available to multiple departments has paid off providing efficiencies for the whole company.
-
The Land group has a visualization of their current owned wells and any can identify prospects nearby.
-
The Surface group can quickly differentiate between operated and non-operated leases managing differing lease requirements with confidence.
-
The Production Accounting group has been able to index the owned percentage and cost coding details to each well, making it easier to maintain these ever-changing details.
-
Operations and Safety have leveraged this central list to maintain regulatory compliance and decrease windshield time through advanced scheduling features that automatically adjust the required inspection depending on the well status.

Connections to Petro Ninja has allowed Torc to see where their wells are, reconcile with the current public data and even view production data.
Pulling the various required datasets together with the corporate well list has allowed Torc to overcome the issues presented with a traditional well list and has seen increased time efficiencies company-wide. Additionally, concentrating their efforts on one corporate well list has allowed Torc to create a reliable, consistent database, moving them one step closer to successful data-driven decisions. All-in-all, the corporate well list has proven to be a powerful asset for Torc and it is still only scratching the surface of what is possible.
With the asset retirement obligations slated to be included in the spring of 2020, the Muddy Boots team and Torc employees foresee more time efficiencies to come.